ABS Handboards Common Processing Methods
ABS is commonly understood to refer to ABS plastic, which is a terpolymer of acrylonitrile, butadiene, and styrene (S). Different resins can be made by adjusting the proportions of the three monomers. In ABS, all three of these elements share the same characteristics. A gives it surface hardness and makes it resistant to chemical corrosion and heat. B improves its pliability and toughness. S gives it the formability and heat resistance of thermoplastic plastics and enhances its electrical characteristics.
ABS plastic has good comprehensive performance, a low price, and a wide range of applications; as a result, it can be described as “tough, hard, and inflexible.” The chemical industry, as well as the mechanical, electrical, textile, automobile, airplane, and shipping sectors, have all found extensive uses for ABS plastics. In the handboards sector, ABS plastic is frequently used for processing and manufacturing handboards. ABS handboards are widely produced in the model handboard market. CNC machining, vacuum laminating, and 3D printing are just a few of the methods that can be used to modify ABS handboards. Which of these three approaches to analyzing abc codes is best, and why? Which qualities distinguish them? At this time, Tianhong Molding will provide a comprehensive overview of the most often used abs processing methods.
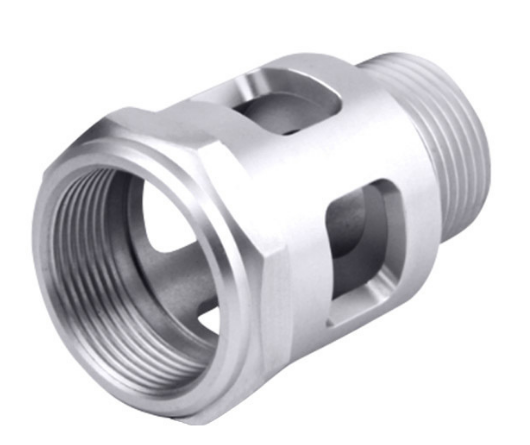
ABS manual CNC processing
Advantages: High precision, generally up to 0.05mm~0.1mm, and a wide range of processing dimensions. Some CNC machining centers can process a two meter long hand board as a whole; Various materials and good surface treatment effect.
Disadvantages: It is charged according to the working hours. For small and complex hand boards, it is not cost-effective to use CNC processing.
Features: High degree of automation, strong adaptability to CNC machining objects, high machining accuracy, stable quality, which can greatly improve machining accuracy, including machining quality accuracy and machining time error accuracy; The repeatability of the processing quality can stabilize the processing quality and keep the quality of the processed parts consistent.
Abs hand board 3d printing processing:
Advantages: High precision, fast printing speed, and complicated printing details.
Disadvantages: Charge according to weight, and the cost of printing large hand boards is high; Processing size is limited; There are few printing materials, mainly photosensitive resin and ABS.
Features: One of the greatest benefits of 3D printing is the time, money, and resources it saves in the long run. We aren’t frightened to make changes to the work, since doing so can make the original product highly functional, but we are afraid of the time wasted in processing and transportation, which will add up to a hefty sum in the next round of changes. Characteristics of 3D printing show that it is possible to produce models and final goods more quickly and with higher quality. If you want high-quality prints, you need to invest in a pricey printer.
Abs manual vacuum double die processing:
Advantages: Low cost, short production cycle, small batch (50-500 pieces) production has advantages.
Disadvantages: Due to the influence of thermal expansion and cold contraction of silicone liquid, the precision is relatively low, usually about 0.2mm; One set of silicone mold can only copy 10 handbooks, and the price is high when the quantity is more than 500.
Features: Reduced expenses and a rapid turnaround time for finished products. The processing cost is substantially lower than CNC processing or 3D printing, and there is less waste. Because of its operability in mold creation, low failure probability, and high repeatability, it can be used in the processing and production of items in small quantities.